In this article, we will be talking about the emerging technologies and trends of tunnel instrumentation and monitoring. From cloud-enabled web data monitoring to non-contact methods for monitoring, there is an emergence of modern technology that is increasingly gaining popularity and is more affordable.
We have seen a rise in a reliable sensor network that promotes fast and effective data representation. This becomes even more crucial in high-risk urban tunneling projects. Moreover, the cost competitiveness of the industry has motivated and promoted the need for more affordable alternatives.
Let’s take a look at the various technologies provided by Encardio Rite for tunnel monitoring, and how they serve the current demand of the industry, along with the emerging trends.
Wired & Wireless Sensor Networks:
(a) SD-12 interface real-time monitoring
Real-time monitoring plays an important role in geotechnical instrumentation and monitoring. For accurate and seamless data collection, advanced automatic data loggers have been designed with built-in GSM/GPRS modems. These have an SDI-12 interface and provide wireless transmission to a remote server.
SDI-12, here, refers to the Serial Digital Interface at 1200 bauds, which is an asynchronous serial communication protocol used to connect and communicate with multiple sensors tied in a daisy chain fashion.
The SDI-12 interface is widely popular as it requires only a single 3-conductor cable to interconnect the sensors and the data loggers in a serial bus. When the power is supplied from the SDI-12 instruments through the SDI-12 bus, there is a route for communication on the bidirectional serial data line between SDI-12 sensors and the datalogger. The cables coming from multiple sensors are joined at the multi-position junction, also known as the switch boxes. At the conclusion, the multicore cables are routed to the data acquisition system.
With the SDI-12 monitoring, you save a notable part of the overall cabling cost.
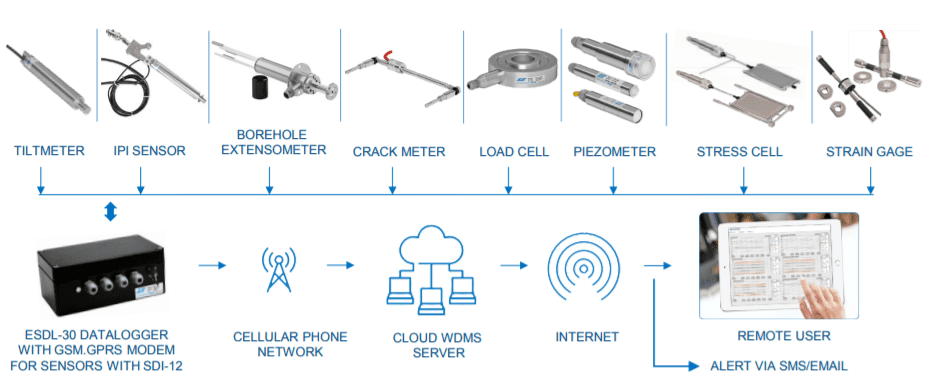
The GSM/GPRS capability of the data loggers allows uploading the recorded data directly to the remote FTP server. You can adjust the device to measure from 5 seconds to 168 hours. Moreover, the data is recorded with the current date, time, and battery voltage.
Communication between the device(PC & Mobile) and the datalogger can either be through a cable or a Bluetooth modem.
(b) Wireless real-time monitoring using RF
The wireless monitoring solution makes use of RF data loggers or nodes that are compatible with a wide array of geotechnical and environmental sensors and RF gateways. Encardio Rite offers an innovative long-range radio network solution that allows real-time monitoring of geotechnical and structural sensors in challenging conditions with reliable data transfer without any delay. The data remains accessible to any authorized user across the globe by logging on to the web-based data management software.
In our end-to-end wireless monitoring system, the sensors are interfaced with the long-range, low-power wireless network through RF nodes that send recorded data to the Gateway with utmost reliability. Gateway uploads the collected sensor data to the central/cloud server.
The long-range radio frequency-based wireless data collection network provides complete automation of monitoring with seamless connectivity in large construction sites, tunnels, and landslide projects. The wireless system eliminates the need for running lengthy cables. It is especially useful at locations where sensors are distributed over wide areas and running cable lengths to long distances can be tricky and/or at locations where construction activity can damage the running sensor cables.

The wireless mesh-based data collection protocol is very useful in tunnels as it provides uninterrupted connectivity. If at any point during the monitoring process, the node cannot reach the gateway directly, the information can still be sent via other nodes in the network. This makes it a very reliable option. All the data collected is sent to the gateway, with each gateway handling up to 50 nodes.
Wireless Monitoring using RF nodes provides a cost-benefit while also reducing the time needed for the monitoring work. Moreover, you can access hard-to-reach locations easily with its remote monitoring techniques.
| Also Read: Rohtang Pass Tunnel Case Study – Geotechnical Monitoring & Instrumentation|
(c) Web Data Monitoring Service
When it comes to online tunnel monitoring, it is crucial and necessary to have Data Management Software that can retrieve the data seamlessly from the SDI-12 data logger, RF Gateway, or ATS control box. The DMS is either public cloud-based or server-based and then works to archive the data in SQL Database. It then further displays the processed data in graphs, tables, and other formats, allowing the authorized personnel to understand it completely.
The Web Monitoring Software is accessible from any type of device that is supported by a web browser, for example, desktop, tablet, PC, laptop, smartphone, etc.
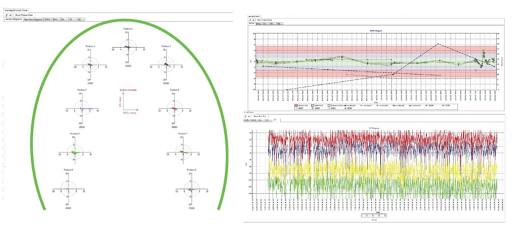
With Data Management Software, you can have an overview of the tunnel section being monitored, along with the position of installed sensors, etc. Hovering over the location will give you details like the last recorded sensor reading, sensor identification tag, and the values of the programmed alert levels pop up in a box. To identify any sensor that may have exceeded the alert level, you will spot a red dot on that location.
Site Administration can set two alarm limits, generally known as “alert level” and “evacuate level”. The DMS can be programmed to send SMS alert messages or emails whenever a sensor level crosses the set mark.
It is also possible to integrate live Tunnel Boring Machine (TBM) data with the monitoring data on the data management software. Lastly, you can also work on generating automatic or manual reports which are covered by the data management software.
Advanced Survey and Monitoring Solutions:
(a) Automatic 3D Deformation Monitoring System
During underground construction, multiple factors like load, aging, etc. may alter the shape or dimension of the tunnel or any structure that is placed in the zone of influence. The real-time 3D deformation monitoring system allows for tracking any change or alteration taking place.
Encardio Rite's deformation monitoring system is equipped with high-accuracy automated total stations (ATS) that are capable of auto-target recognition without any need for human interference.
The Automated Total Stations are each provided with a control box which includes a computer running special software. The control box looks after the total station while managing the frequency of measurements, application of the filters of acceptance or repetition, addition or subtraction of monitoring benchmarks, the atmospheric corrections in distance measurements, the calculation, and repositioning of the total station, etc.
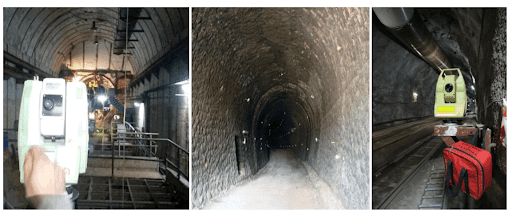
The Automatic 3D Deformation Monitoring System can be simply and remotely re-configured or controlled after the installation at the site. The collected data is transmitted to a cloud/remote server or computer with the help of GSM/GPRS. It is also adept enough to provide reliable, real-time data, without any error or delay.
In case any sensors cross the critical alert level, the authorized personnel are immediately informed via an SMS or email. Moreover, come rainfall, storms, or heavy winds, the ATS and control boxes are designed to stand tall during severe conditions stretching across a wide temperature range.
The Monitoring System is also equipped with in-built batteries that perform for several hours without external power. In case the mains power is not accessible, the systems can also be powered by solar panels.
| Also Read: Instrumentation & Structural Monitoring of Dams |
(b) Laser Scanning
An advanced technology that has been gaining popularity in the geotechnical and tunnel monitoring arena is Laser Scanning. Known to reduce time, cost, and effort tremendously, it provides a very clear and exact description of complex shapes and surfaces. This, in turn, assists in preparing complete geometric documentation of existing conditions.
The Laser Scanning technology comes in handy for surveying locations that are inaccessible or very hard to reach. It is based on the dense mapping of 3D coordinates where it is surveyed, taken at speeds ranging from a few thousand up to a million points per second.
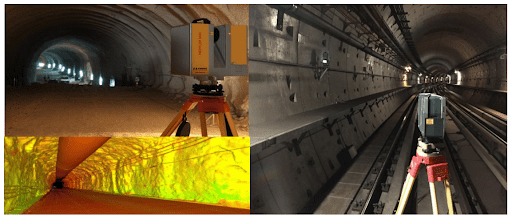
Laser Scanning also gives multiple options to the user according to the object, allowing the monitoring to be either airborne or terrestrial, static or mobile, autonomous or in combination with other standard topographic methods.
Recent developments, especially in the software, have made it a very convenient and cost-effective tool for accurate tunnel monitoring & deformations in 3D.
(c) Aerial Mapping using Unmanned Aerial Vehicles (UAV/Drone)
Coming to another advanced technology in tunnel monitoring & instrumentation is the use of Unmanned Aerial Vehicles (UAV)/Drones. Tunnel Construction sites which are slightly more complicated and complex than others need a high degree of analysis but are restricted as they are difficult to reach or gain access to. In such cases, UAV/Drones are really helpful. Let’s see what it is all about.
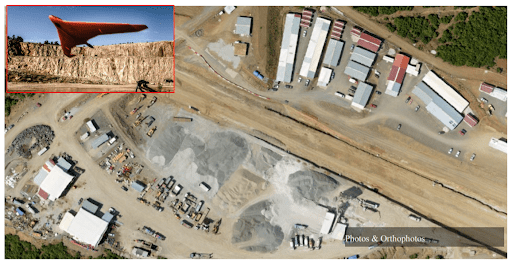
UAVs or Drones are remotely piloted aircraft that are programmed to follow a pre-decided route for take-off, flight, and landing. The unmanned aircraft feature HD/IR/Thermal cameras/laser scanner that is capable of taking images/videos/point clouds over a defined area at a specified height.
Using Aerial Vehicles proves to be a smarter and safer choice as these devices can capture a video, or scan for cracks, corrosion, defects, etc. in an area that would otherwise require a human being suspended using a rope/harness, etc.
Moreover, Large sites with complex structures require aerial surveys which avoid expensive ground-based surveys. The technology also becomes beneficial during the construction process as it becomes easier to maintain a true picture of the site.
Results from UAV/drone are in the following forms:
- Photos & Orthophotos
- Mesh 3D Models & Texture 3D Models
- Drawings
- Videos – Presentations
- Contour maps
- Slope maps
- Area – Volumetric calculations
The technology that has recently sprouted in the geotechnical instrumentation and survey field plays a very crucial role in design verification and assumption, construction field management, and the long-term behaviour of tunnels. Moreover, it also provides safety for the surrounding structures and communities that fall in the zone of influence.
With this, we come to the end of our article. For more such interesting articles on geotechnical monitoring and civil engineering, keep watching this space.